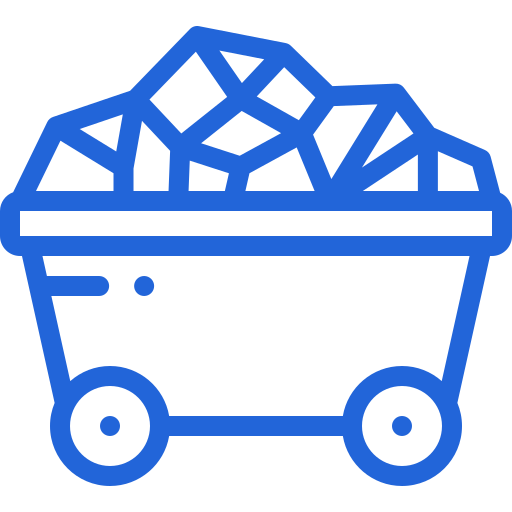
Resource Recovery Lithium
UNLOCKING LITHIUM THROUGH SUSTAINABLE, EFFICIENT BRINE CONCENTRATION
Gradiant’s new solution enhances the impact of the sustainable lithium extraction process for reduced time-to-market and environmental footprint. The technology enables high levels of lithium concentration in a fraction of the time required by conventional methods (days instead of years) while reducing carbon emissions, energy consumption, and capital costs compared to thermal-based technologies. RO Infinity concentrates process streams close to saturation limits, reducing or eliminating the need for downstream evaporators or ZLD systems. This technology integration can be applied to new lithium mineral extraction and production sites, opening opportunities to untapped production regions and existing production operations.
Fast Facts
Location: Clayton Valley, Nevada, USA
End User: SLB
Solution: Brine Concentration
Industry: Mining (Lithium)
Feedwater Source: Subsurface Brine
Technology: RO Infinity with CFRO
System Configuration: Single Train, Multi-Stage
Commissioning Date: 2023
Delivery Model: Design-Build (DB),
Operate & Maintain (O&M)
The Challenge
The surging global demand for lithium and other battery minerals, driven by the rapid adoption of electric vehicles and energy storage solutions, presents a formidable challenge in identifying sustainable supply sources. Producers are grappling with deploying new, more efficient, and environmentally sustainable technologies. In response to this challenge, SLB (formerly Schlumberger) has developed a direct lithium extraction (DLE) and production flowsheet. In this flowsheet, Gradiant’s technology concentrates the lithium solution and generates fresh water, a critical element in sustainable lithium production from brine. This solution is now deployed at SLB’s Nevada site, marking a pivotal step towards meeting the escalating demand for lithium in a more sustainable manner.
The Solution
DLE uses chemical and physical processes to extract lithium from saline brine sources or other unconventional deposits. DLE technologies include ion exchange, adsorption, solvent extraction, and membrane separation. DLE is suitable for lithium resources in regions with a wide range of brine compositions and environments, making it an effective alternative in areas where evaporation ponds may not be viable.
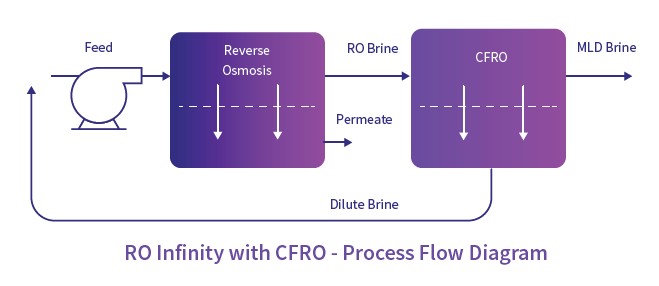
Gradiant has designed, built, and is now operating an RO Infinity with CFRO system to concentrate lithium up to 15 times to enable higher lithium recovery. The innovative brine mining process concentrates the lean liquors to maximize the efficiency of lithium production at the site. The system is fully integrated into the SLB flowsheet and ensures that brine is treated and pre-concentrated before the CFRO step. CFRO is also used to generate water for the DLE process. The system operates at normal RO pressures, allowing standard commercially available membranes and components to be used. RO Infinity’s high system recovery rates serve to reduce downstream evaporator size and cost and, in some cases, remove the need for them entirely.
Squeezing every last drop of water from the DLE process is highly important to SLB, given the site’s remote location in an arid region with limited access to water. A second RO Infinity system is available at the site to produce fresh water from the DLE waste stream. This minimizes or can avoid the need for groundwater withdrawals or the need to truck in water from off-site.
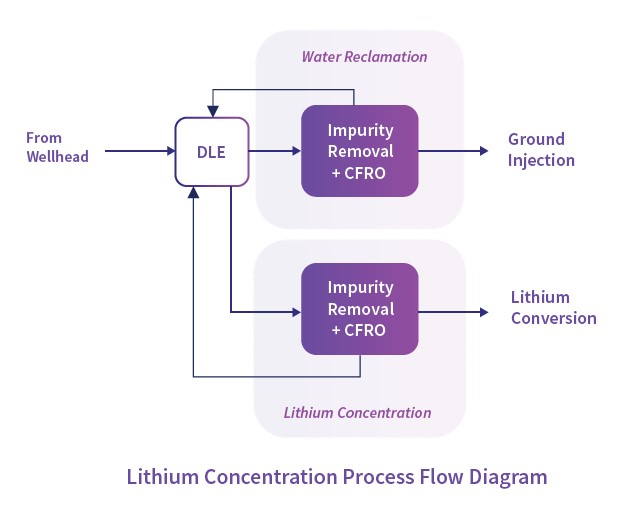
The Benefits
Gradiant’s new solution enhances the impact of the sustainable lithium extraction process for reduced time-to-market and environmental footprint. The technology enables high levels of lithium concentration in a fraction of the time required by conventional methods (days instead of years) while reducing carbon emissions, energy consumption, and capital costs compared to thermal-based technologies. RO Infinity concentrates process streams close to saturation limits, reducing or eliminating the need for downstream evaporators or ZLD systems. This technology integration can be applied to new lithium mineral extraction and production sites, opening opportunities to untapped production regions and existing production operations.
Impact Stats
15x
Concentration Factor
60%
Cost Savings vs. Traditional Technologies
Up to 100%
Water needs met for DLE process through reuse
Legal Disclaimer
This document is for general information only. No warranty or guarantee whatsoever is given or implied and Gradiant is not bound by or liable for or by the information contained herein. Customer has the sole responsibility to determine whether the information in this document are appropriate for Customer’s use, including without limitation actual site, geographical, and plant conditions, specifications, requirements, disposal, applicable laws and regulations. This document is the intellectual property of Gradiant, including but not limited to any patent or trademark contained in this document. Distribution of this document is not and does not imply any transfer of Gradiant’s intellectual property.
Gradiant, the Gradiant Logo, and all trade and service marks denoted with ™ or ® are owned by affiliates of Gradiant Corporation unless otherwise noted. © 2023 Gradiant.