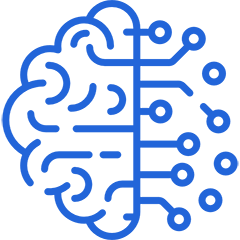
SmartOps AI
MACHINE LEARNING SAVES ENERGY FOR LARGE SWRO IN THE MIDDLE EAST
Turing, a Gradiant company, was able to use machine learning to apply its patented SmartOps technology to save up to 5% energy, the equivalent of hundreds of thousands of dollars, at a large seawater reverse osmosis plant in the Middle East, while remaining within strict design limits. An international performance measurement and verification protocol was applied to confirm testing results.
Fast Facts
Location: Middle East
End User: ENGIE
Solution: Seawater Desalination
Industry: Municipal & Infrastructure
Feedwater Source: Seawater
Technology: SmartOps AI
System Configuration: 25 + 1 trains, Pelton wheel
System Capacity: >200,000 m3/day
Online Date: 2021
Delivery Model: Software-as-a-Service (SaaS)
The Challenge
Our client, ENGIE, a French multinational electricity utility, faced challenges of high energy consumption at a large-scale seawater reverse osmosis (SWRO) desalination plant in the Middle East. Desalinating seawater is energy-intensive for a few key reasons. Desalination typically requires a significant amount of energy to pump seawater, pressurize it, and force it through filtration or membrane systems to remove salt. The energy cost is a major contributor to the overall expense of desalination. Optimizing the performance of multiple reverse osmosis (RO) trains also presents a daunting challenge for operators
as it is virtually impossible to determine the best operating parameters and membrane replacement frequency to maximize energy savings.
The Solution
Gradiant’s SmartOps technology is a powerful software platform that uses machine learning to optimize plant performance and manage assets efficiently. The technology takes into account various input and output parameters, ensuring that facilities meet operating design standards and mechanical limitations, while reducing energy consumption and maintaining water quality and production targets. It’s particularly effective in optimizing the flow of water across reverse osmosis trains with varying efficiencies.
By harnessing the power of machine learning AI algorithms, SmartOps can enhance and predict plant operations, leading to immediate improvements in productivity, cost savings, and reduced carbon and water footprints.
A historical data audit showed that the SmartOps digital technology could achieve energy savings of up to 5%, with a maximum recovery rate of 48% for a plant using a Pelton wheel and manual feed control valve.
To verify these energy savings, Gradiant’s Turing employed a simulation model based on ISO International Performance Measurement and Verification Protocol (IPMVP®) to predict what the energy use would have been under standard conditions. This confirmed the energy savings with the client.
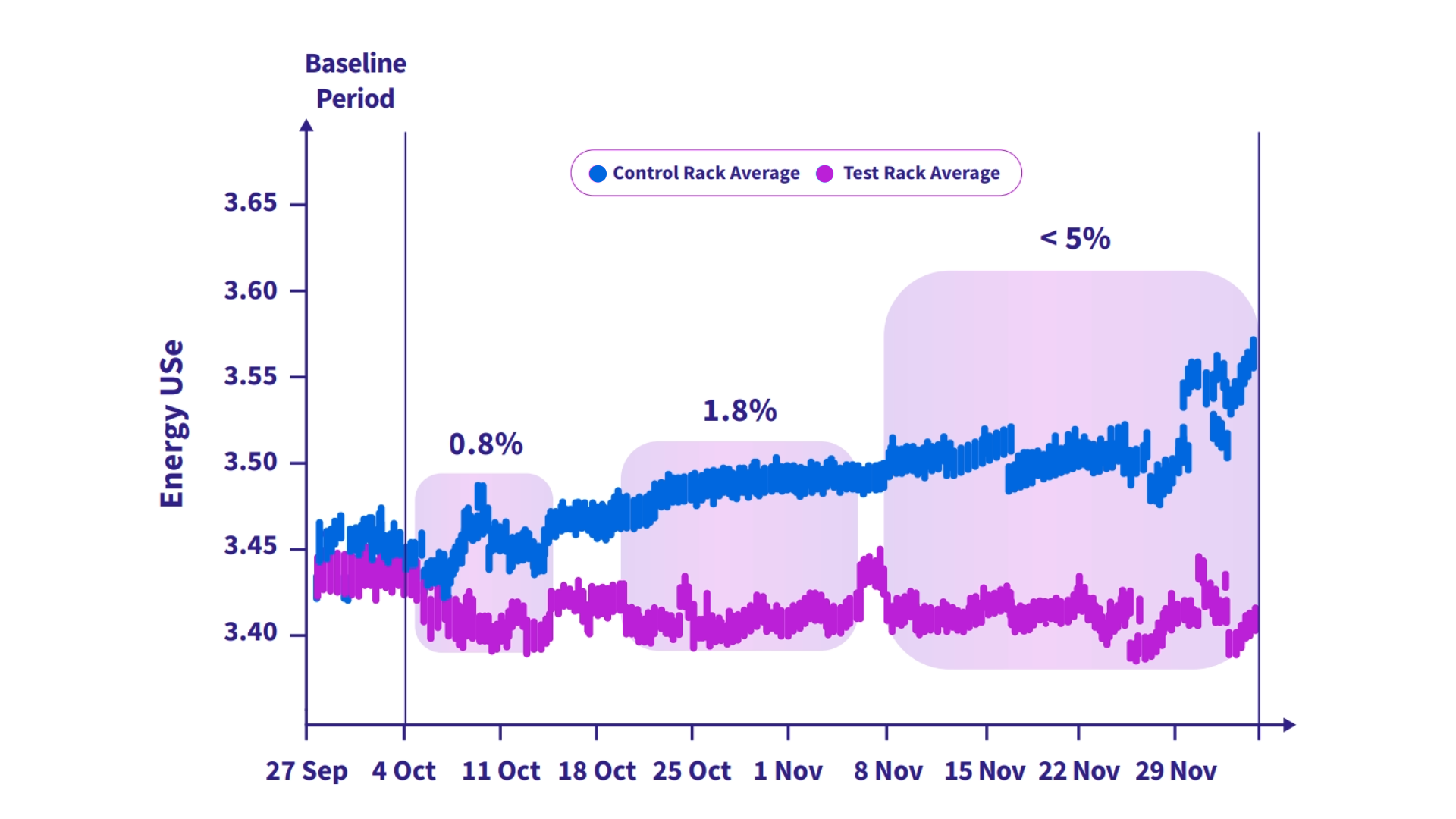
The Benefits
Machine learning is a game-changer for plant owners and operators, helping them efficiently control systems and make decisions based on data. Simple daily recommendations for settings allow operators to easily input the best values, so they can focus on providing high-quality water to the ENGIE facility’s 600,000 end-users. Achieving these savings doesn’t require any extra equipment or hardware investments.
ENGIE’s large-scale (SWRO) facility remains a leader in machine learning technology adoption. Its success has become a model for many plants worldwide, allowing them to replicate these benefits. Machine learning integration not only saved a lot of energy, but also improved system control and data-driven decision-making, benefiting both plant operators and managers.
Gradiant’s SmartOps Digital technology continues to revolutionize the seawater desalination industry, leading the way for other plants around the world to save energy and gain similar advantages.
Impact Stats
5%
Energy Savings
48%
Maximum
Recovery Rate
>200,000 m
3
Daily System Capacity
<5%
Differential
Pressure Increase
99.95%
Uptime
12M
Tonnes Co
2
Saved Every Year
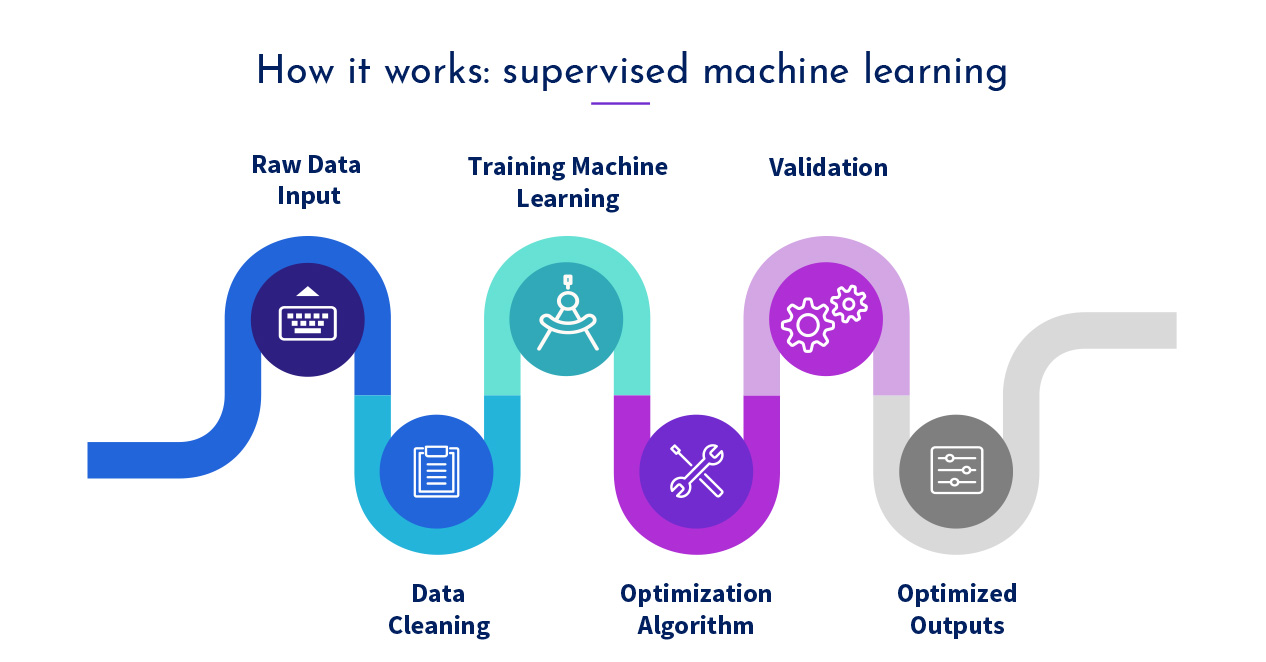
Legal Disclaimer
This document is for general information only. No warranty or guarantee whatsoever is given or implied and Gradiant is not bound by or liable for or by the information contained herein. Customer has the sole responsibility to determine whether the information in this document are appropriate for Customer’s use, including without limitation actual site, geographical, and plant conditions, specifications, requirements, disposal, applicable laws and regulations. This document is the intellectual property of Gradiant, including but not limited to any patent or trademark contained in this document. Distribution of this document is not and does not imply any transfer of Gradiant’s intellectual property.
Gradiant, the Gradiant Logo, and all trade and service marks denoted with ™ or ® are owned by affiliates of Gradiant Corporation unless otherwise noted. © 2023 Gradiant.